Introduction to Protein Powder and Its Packaging
Protein powder is a powdered food that replaces traditional meals, providing necessary nutrition and energy. Its packaging must meet the requirements of protecting the product, being convenient for carrying and use, and maintaining the product’s freshness and hygiene. The packaging must not only be aesthetically pleasing but also ensure the safety of the product during transportation and storage.
Pain Points of Traditional Protein Powder Packaging
Traditional protein powder is mainly packaged manually, which involves labor-intensive processes such as material handling, weighing, filling, and sealing. This often consumes a lot of manpower and is prone to errors, with the following pain points.
2.1 Low Packaging Efficiency
Traditional manual packaging methods have significant limitations in speed and efficiency, especially when facing the demands of large-scale production. The speed and efficiency of manual operations cannot meet the needs of modern production, which not only limits production volume but also increases production costs.
2.2 Inaccuracy in Packaging
When manually filling protein powder, due to human factors, it is difficult to ensure that the weight and quality of each bag of product are completely consistent. This inconsistency may lead to a non-uniform consumer experience, affecting brand reputation and product repurchase rates.
2.3 Contamination Issues During Packaging
In manual packaging processes, due to direct contact with the product, operators may inadvertently introduce contaminants into the packaging, which not only affects the hygiene and safety of the product but may also violate relevant food safety regulations.
2.4 Inconsistent Package Sizes and Shapes
Manual packaging finds it hard to ensure that the size and shape of each package are completely consistent, which affects the product’s aesthetics and market competitiveness. In the retail segment, a uniform packaging appearance is crucial for brand image.
2.5 High Labor Costs and Physical Demand in Packaging
Manual packaging requires a large amount of human resources and is physically demanding, which not only increases the company’s labor costs but may also lead to employee fatigue and production accidents, affecting overall production efficiency and safety.
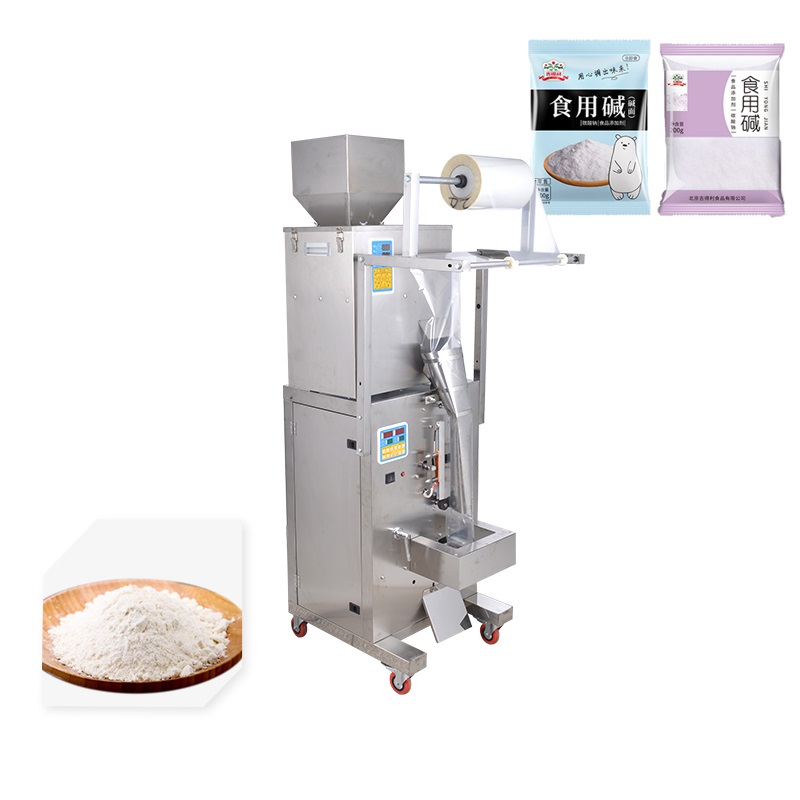
Solutions to the Above Pain Points
3.1 Enhancing Automation Levels
By introducing automated protein powder packaging machines, manual operations can be significantly reduced, improving packaging speed and efficiency to meet the demands of large-scale production.
3.2 Precise Measurement Technology
Integrating an automatic quantitative weighing module in the protein powder packaging machine, using advanced feeding systems and measurement technology, ensures that the filling amount of each bag of protein powder is accurate, enhancing the consistency of product quality.
3.3 Strengthening Hygiene and Safety Control
Sealing and sealing functions ensure the hygiene and safety of the packaging process, preventing the entry of contaminants and protecting the freshness and hygiene standards of the product.
3.4 Standardizing Package Sizes and Shapes
Using adjustable parameters of the packaging machine, standardize the size and shape of the packages to enhance the uniformity of the product’s appearance and brand image.
3.5 Reducing Dependence on Labor
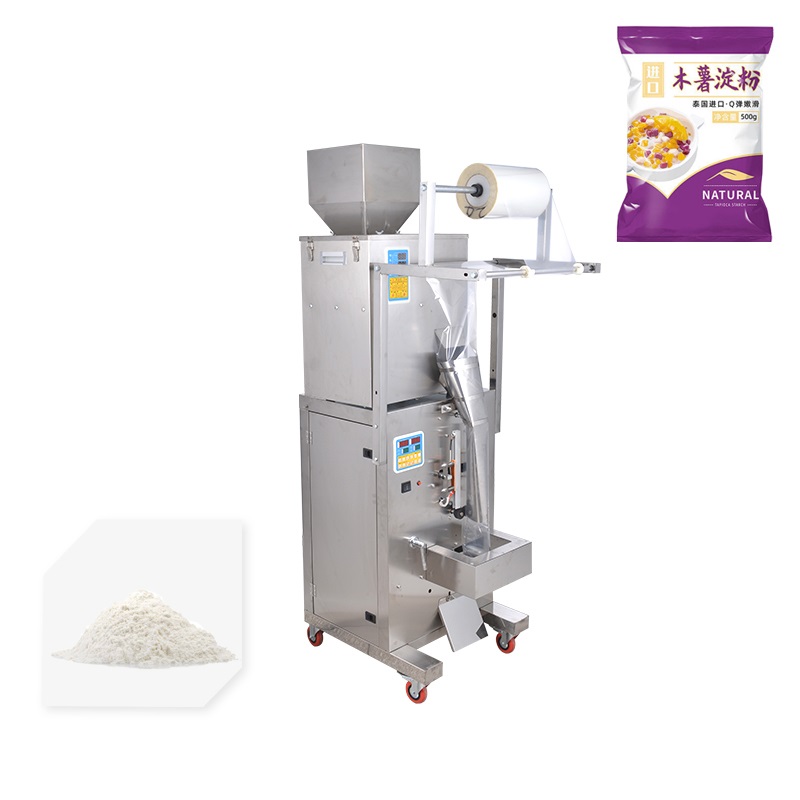
Recommended Machine Solutions
Reducing manual operations and physical labor, improving work efficiency through automation technology, while also reducing labor costs and potential safety risks.
4.1 High-Efficiency Automated Packaging Machines
It is recommended to choose packaging machines that can automatically complete feeding, measuring, sealing, and labeling processes to improve overall production efficiency.
4.2 Precisely Controlled Measuring Systems
Select packaging machines equipped with high-precision measuring systems to ensure that the filling amount of each bag of product is accurate and maintain the consistency of product quality.
4.3 Hygienic and Safe Packaging Design
Recommend using packaging machines with good sealing and sealing functions to ensure the hygiene and safety of the product, preventing contamination.
4.4 Customizable Package Sizes and Shapes
Choose packaging machines that can adjust package sizes and shapes according to product needs to meet the demands of different markets and consumers.
4.5 Automation Reducing Physical Labor
Recommend using packaging machines that reduce the need for manual operations to lower physical labor, and improve employee job satisfaction, and production safety.
Conclusion
Protein powder packaging machines solve many pain points of traditional packaging methods through automation technology, not only improving packaging efficiency and accuracy but also ensuring product hygiene and safety, and reducing labor costs and physical labor. Choosing the right packaging machine solution is crucial for enhancing the production efficiency and quality of protein powder.