Automatic vertical granule packaging machines play a significant role in industries such as food, chemical, and pharmaceutical, where the centrifugal disc feeding part directly impacts the efficiency and quality of pouch packaging. Machine malfunctions can not only decrease production efficiency but also affect product quality. Therefore, understanding common packaging machine troubleshooting and solutions is crucial.
I. First, Exclude Inappropriate Packaging Machine Applications
When purchasing an automatic vertical granule packaging machine, understanding its suitable range is essential. This includes the size, shape, humidity, and concentration of the liquid of the packaged items. The correct choice can prevent subsequent operation problems and ensure smooth packaging operations.
II. Common Failures and Solutions
Failure One: Uneven Feeding
Symptoms: During the packaging process, the product distribution in the pouch is uneven, with some areas having too much material and others too little.
Cause Analysis:
The speed setting of the centrifugal disc is inappropriate, preventing the material from being evenly dispersed.
The characteristics of the material (such as shape, size, and density) do not match the current feeding speed or method.
The disc surface is worn or has foreign objects, hindering the normal flow of the material.
Solutions:
Adjust the speed of the centrifugal disc to suit the material characteristics.
Clean the disc surface to ensure no foreign objects are present.
Adjust the feeding port design or use auxiliary tools based on material characteristics to help distribute the material evenly.
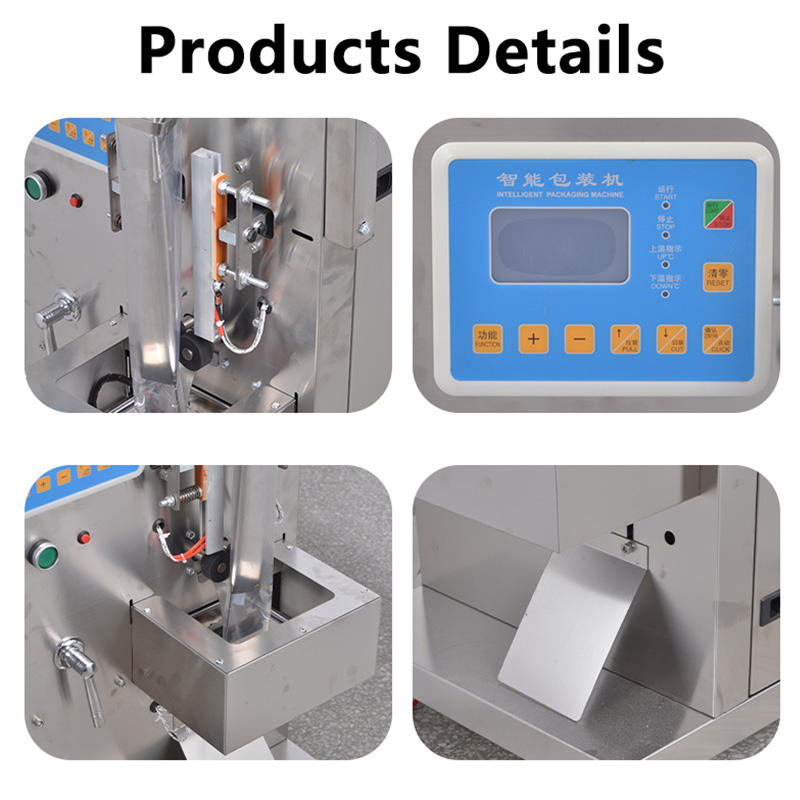
Failure Two: Feeding Clogging
Symptoms:
The material cannot flow smoothly through the feeding port, causing clogging and affecting the packaging process.
Cause Analysis:
The material is too moist or sticky, forming clumps.
The feeding port size is not reasonably designed and is too small for large granule materials.
Foreign objects mixed in the material hinder the normal feeding process.
Solutions:
Control the humidity of the material to avoid excessive moisture.
Check and appropriately enlarge the feeding port size to ensure all materials can pass through.
Regularly clean the feeding port to prevent foreign objects from entering and keep it unobstructed.
Failure Three: Unstable Feeding Quantity
Symptoms:
During the packaging process, there is a significant variation in the amount of material fed each time, directly affecting product quality control and consistency.
Cause Analysis:
The control system parameters are not set properly, leading to imprecise control of the feeding quantity.
Sensors or detectors fail, unable to correctly feed the control system’s material status.
The material has poor flowability and easily accumulates during the feeding process.
Solutions:
Recalibrate the control system to ensure precise control of the feeding quantity.
Check and replace any damaged sensors or detectors to ensure accurate feedback.
Improve material flowability through preprocessing methods to reduce accumulation.
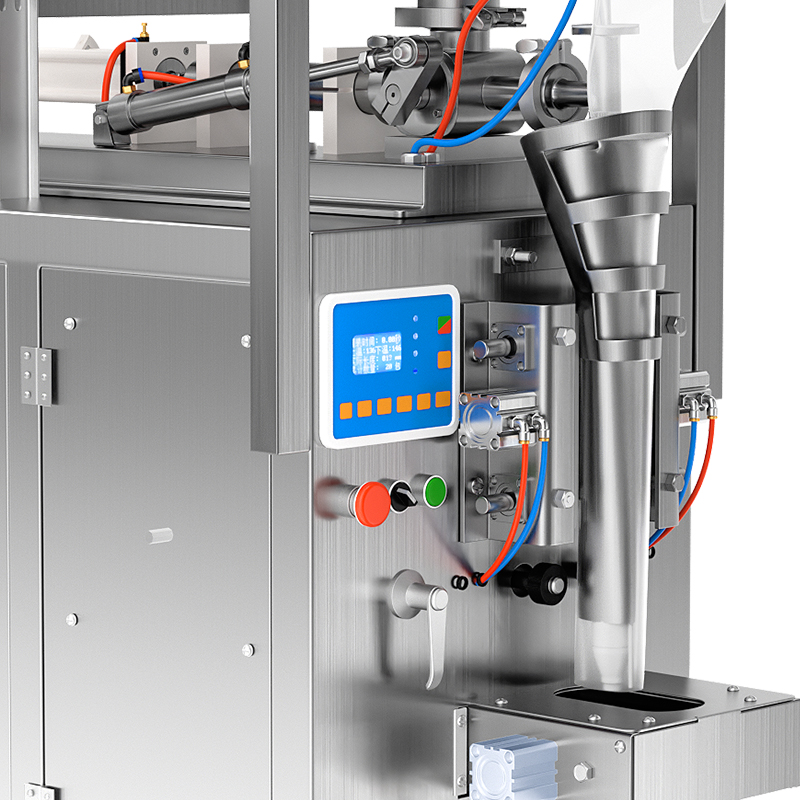
Failure Four: Abnormal Noise Increase
Symptoms:
During equipment operation, the noise level significantly increases, which not only affects the working environment but may also be an early signal of equipment problems.
Cause Analysis:
Parts wear or loosen, causing additional vibration and noise.
Bearings lack proper lubrication, increasing friction and noise.
The equipment is not stably installed, causing abnormal vibration during operation.
Solutions:
Regularly inspect the equipment, tighten all loose screws and other connecting parts to reduce noise and vibration.
Add an appropriate amount of lubricating oil to bearings and other moving parts to reduce friction.
Check the installation of the equipment and, if necessary, readjust to ensure stable operation.
III. Conclusion
Regular maintenance is crucial for automatic vertical granule packaging machines, as it not only prevents malfunctions but also extends the equipment’s lifespan. Operators should receive professional training to understand the working principles of the equipment and common troubleshooting methods to respond quickly to issues. Proper operation and maintenance are key to improving production efficiency and product quality. It is recommended that readers regularly inspect the equipment to maintain its optimal performance. For further consultation on equipment maintenance and troubleshooting, please contact our technical support team.