This article provides a detailed introduction to the working principle and advantages of net weight fillers. These machines ensure that the weight of the product filled in each container meets expectations through an accurate electronic scale. The article explores the workflow of this filling technology, including the measurement of the empty bottle weight, product filling, final weight measurement, and data collection. Additionally, it discusses the application of net weight fillers in automatic packaging and how they enhance production efficiency and product quality. Finally, it emphasizes the importance of net weight fillers in modern manufacturing and the potential savings they offer to manufacturers and end consumers.
Understanding the Working Principle of Net Weight Fillers
Net weight fillers are precision equipment designed to ensure the accurate weight of products filled within containers. Their operation is akin to that of an advanced electronic scale, measuring the quantity of product filled in each container.
Initial Setup
When an empty container is placed on the filler’s load cell, the machine first measures the container’s weight, known as the tare weight. This weight is crucial for determining the net weight of the product to be filled.
Filling Process
Once the tare weight is recorded, the filler begins to fill the container. The product is filled using laminar flow technology, ensuring a smooth and consistent flow, reducing the potential for foaming, and ensuring accurate filling.
Monitoring and Adjustment
During the filling process, the filler continuously monitors the weight and adjusts in real time to maintain the desired net weight. This dynamic adjustment is essential for compensating for changes in product properties due to variations in temperature and pressure.
Final Weight Measurement
After filling, the filler measures the final weight of the container with the product. The net weight of the product is calculated by subtracting the tare weight from the final weight.
Data Collection
Net weight fillers collect data on each filling cycle, providing valuable information for quality control and process optimization.
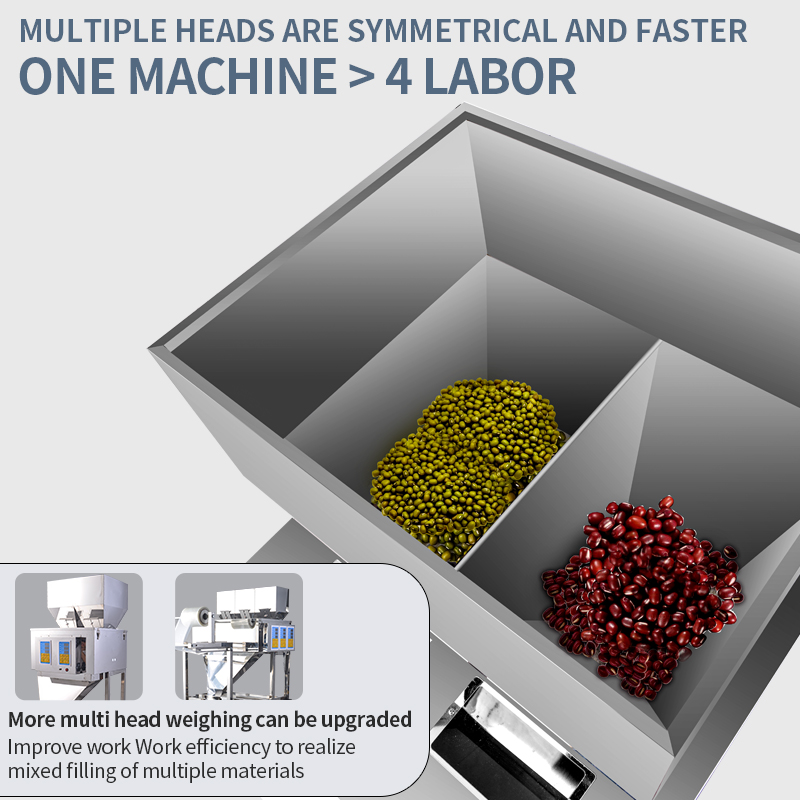
Advantages of Net Weight Fillers
Accuracy
They offer unparalleled filling precision, ensuring consistent weight across all filled containers.Flexibility: These fillers can handle various container sizes and product types, making them suitable for diverse filling requirements.
Automation
They are designed for easy integration into automated production lines, reducing manual intervention and increasing efficiency.
Maintenance
Net weight fillers are user-friendly for maintenance, allowing for quick troubleshooting and minimal downtime.
Applications and Design Considerations
Net weight fillers are commonly used in industries such as food, cosmetics, convenience goods, samples, hardware, and toys due to their precision and adaptability. They offer both automatic and semi-automatic configurations, with the latter providing more manual operation during the filling process.
The design of net weight fillers prioritizes hygiene and ease of cleaning, making them suitable for food and beverage applications. They are also built to be robust and reliable, with features that prevent product wastage and ensure a sanitary filling environment.
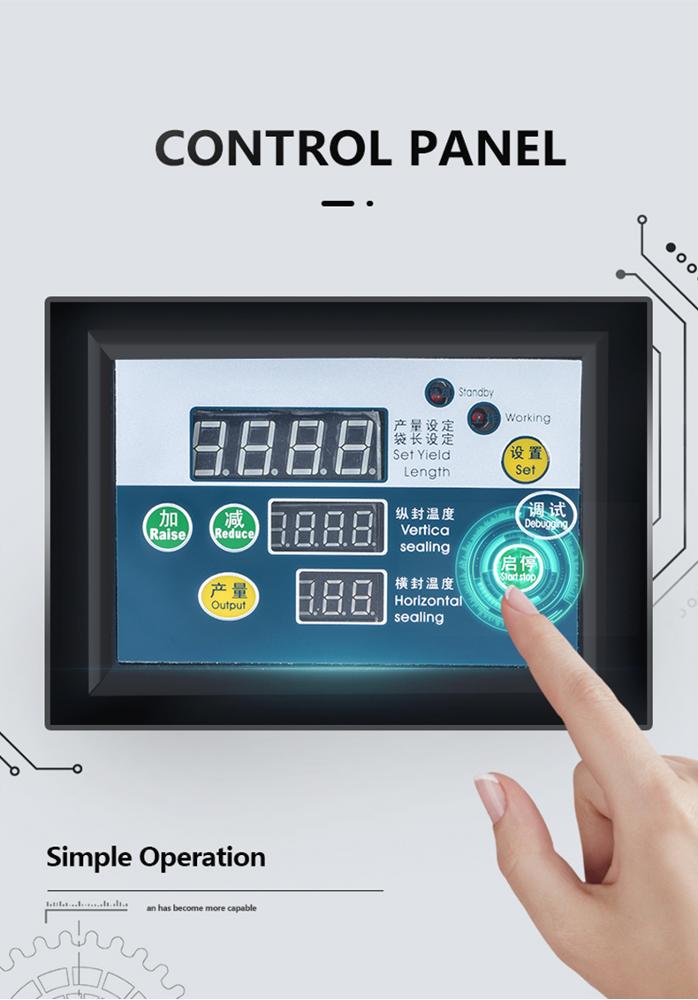
Conclusion
In summary, net weight fillers are a critical component of modern filling operations, providing the high level of precision and efficiency necessary to maintain product quality and consumer satisfaction. As the manufacturing industry continues to evolve, the role of net weight fillers in ensuring product consistency and reducing waste becomes increasingly significant. Their ability to adapt to various product types and container sizes, coupled with their automation capabilities, positions them as a valuable asset in the production process. Furthermore, the potential cost savings they offer can be passed on to end consumers, making net weight fillers not only a practical choice for manufacturers but also a beneficial investment for the broader market.